Стартъп прави вятърната енергия по-достъпна с роботи за 3D принтиране
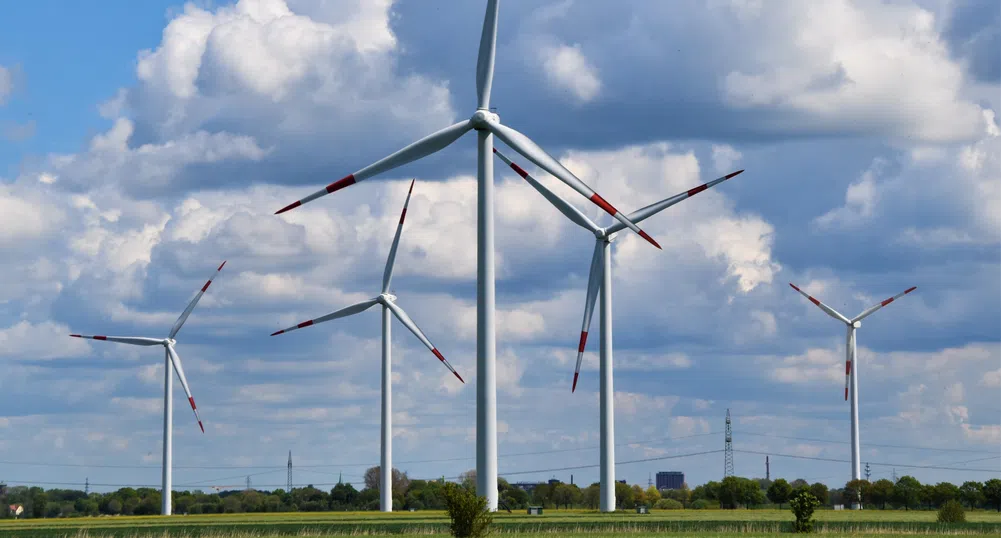
Едно от предизвикателствата при изграждането на нов вятърен парк е транспортът - ако лопатката на вятърната турбина е дълга 60 метра или дори повече, тя няма как да се придвижи лесно по обществените пътища.
Всъщност преместването на една вятърна турбина може да отнеме цяла година планиране, а трудността на доставката повишава цената на вятърната енергия, пише Fast Company, но един стартъп е разработил система за използване на 3D принтиране и роботика за производство на вятърни турбини на мястото, където ще се използват.
"Искаме да можем да произвеждаме основите, кулата и лопатките на място, което е радикална промяна в сравнение с начина, по който това се прави днес", казва Амолак Бадеша, главен изпълнителен директор на стартъпа Orbital Composites, пред онлайн изданието.
Компанията е разработила нова технология, която ѝ позволява да отпечатва композитни материали с висока скорост. В момента вятърната индустрия използва трудоемки производствени техники.
"Повечето хора не знаят това, но всъщност в САЩ са останали нула фабрики за производство на вятърни перки", казва Бадеша. "Преди имахме повече, но всички те бяха изнесени заради това колко ръчен е нужен в този процес. За да се възползват от стимулите за местно производство, някои компании докарват лопатките в САЩ само за шлайфане и боядисване“.
Orbital вече използва технологията си за отпечатване на дронове и части за сателити. За изработването на лопатки за вятърна турбина тя ще отпечата гигантска 3D форма. Цялото оборудване може да бъде доставено до обекта в транспортни контейнери.
Като се елиминира необходимостта от преместване на крайния продукт, е по-лесно да се правят по-дълги лопатки - а колкото по-голяма е лопатката, толкова повече енергия може да произведе турбината, което намалява цената на енергията. Използването на 3D принтиране също така помага за намаляване на разходите, пише още Fast Company и цитира Бадеша, който казва:
"Когато правите толкова големи структури, разходите ви всъщност се определят от материалите. Традиционните процеси са много разточителни."
Като добавя само точното количество необходим материал, адитивното производство елиминира тези отпадъци и оптимизира разходите с до 25%. Производството на място пък може да намали разходите с още 10% до 25%.
Инженерите разработват и процеси за 3D отпечатване на основи и кули за вятърни турбини. В крайна сметка процесът може да принтира и други компоненти, включително магнити, за които в момента се разчита на редки вносни материали, предимно изнасяни от Китай.
Все пак на първо място ще бъдат вятърните перки. При първата си демонстрация по-късно тази година екипът ще отпечата почти 30-метрова вятърна перка, която ще бъде тествана за ефективност.
През следващата година, в сътрудничество с Министерството на енергетиката на САЩ, компанията планира да тества робот за 3D принтиране, който може да се движи напред-назад по кабелна система, докато създава лопатките.
"Това ни позволява да достигнем мащаба от над 100 метра, което означава, че не се нуждаем от обширна инфраструктура, за да направим тези лопатки", казва Бадеша.
Следващата лопатка, която ще бъде тествана, ще е дълга 50 метра, последвана от лопатки в реален мащаб, които са дълги почти колкото игрище за американски футбол. В крайния продукт ще се използва рециклируем материал - повечето от сегашните лопатки за вятърни турбини не могат да се рециклират.
"Ние не само намаляваме нужния материал, но и ще рециклираме този материла и ще го използваме повторно надолу по веригата", акцентира в заключение Бадеша.